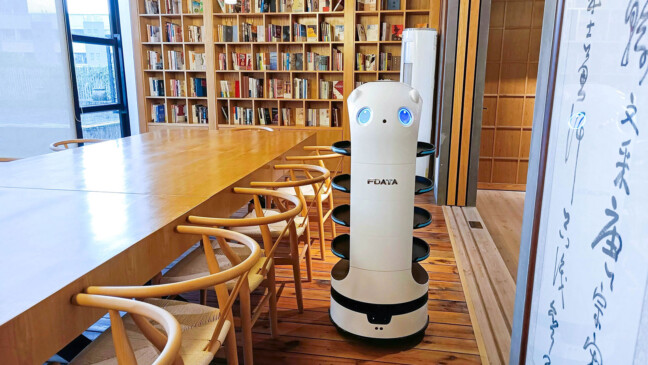
06.03.23
Passivation is a chemical oxidation process. It forms a very thin, transparent passive layer of chromium trioxide (Cr2O3) on the stainless-steel surface, which adheres very strongly to the stainless-steel surface. A passive layer cannot be seen by the naked eye. A passivated surface looks the same as a non-passivated surface.
Stainless steel is widely used in the pharmaceutical and food industries due to its excellent corrosion resistance. Only the high-alloy stainless steels according to DIN EN 10027-1/-2 are approved for use in the pharmaceutical industry. The best-known steel grades in this standard are as follows:
These three stainless steel grades form a protective oxide layer (passive layer) of chromium oxide, more precisely chromium trioxide (Cr2O3), on the surface without additional treatment. During the manufacturing process of sheet steel, steel pipes or other steel parts, this passive layer can become contaminated or damaged, which immediately leads to a decrease in corrosion resistance. For this reason, cleaning and passivation should be carried out after the processing and installation of a stainless-steel surface in the pharmaceutical and food industries. In the following, this article explains how such passivation can be carried out.
Passivation is a chemical oxidation process, which is described in the two standards AMS2700F and ASTM A967. Passivation forms a very thin, transparent passive layer of chromium trioxide (Cr2O3) on the stainless-steel surface with a thickness of 1 to 3 nanometers, which adheres very strongly to the stainless-steel surface. A passive layer cannot be seen by the naked eye. A passivated surface looks the same as a non-passivated surface.
The passive layer has a very high density, so that the steel below the passive layer cannot oxidize further. The passive layer forms a protective film and separates the chromium steel from oxygen and prevents further oxidation.
The natural passivation can be triggered and improved by a further passivation process on the steel surface. In this process, a passivating agent is used. This agent builds and improves the chromium oxide layer so that it becomes uniformly thick and dense. At the same time, the passivating agent removes foreign iron, iron filings, grinding residues, mixed iron crystals or iron slag. These residues must be removed, as they may not be passivatable, may not adhere to the passivated surface and may lead to corrosion.
A high chromium content in the metal, above 12%, leads to a better passive layer. Because of its lower density than iron, chromium is thermodynamically more stable, very reactive as a base metal and has a strong negative electrochemical potential. Therefore, it forms a stable protective layer on the steel surface. The following diagram shows that more than 18% chromium content insignificantly improves the passivation effect.
A molybdenum content of more than 2% protects the passive layer from more aggressive oxidizing agents such as oxygen and also from oxidizing acids.
A nickel content of more than 8% also protects the passive layer from strongly oxidizing media, such as compounds containing chloride.
An increased temperature during passivation reduces the passivation time, but the passive layer does not become thicker or denser. The cleaning effect of iron particles is also accelerated at increased temperature.
Very high temperatures caused by welding, annealing, or tempering destroy or damage the passive layer.
In pure water and elevated temperature of 80°C, iron diffuses through the passive layer to the metal surface. Pure water has a pH of 7.0 at room temperature. When the temperature is increased to 80°C, the pH drops to 6.3 and at 120°C to 6.0. As a result, the diffused iron begins to form an oxide, which is visible on the metal surface as a rouging film and is called hematite (Fe3O4). If the temperature in a steam cycle rises even higher, iron diffusion is enhanced, and corrosion resistance decreases further. At a temperature higher than 120°C, the diffused iron oxidizes to a black magnetite (Fe3O4) layer, which is also called blacking.
Carbon dioxide processes: an increased CO2 concentration leads to a decrease in pH. This can lead to destabilization of the passive layer, especially in hot systems and high temperatures.
Nitrogen processes: oxygen is displaced in nitrogen systems. The lack of oxygen prevents repassivation in places where the passive layer is damaged. Filling the system with an aggressive medium can lead to severe corrosion locally, such as pitting corrosion when hydrochloric acid or other chlorine-containing media are used continuously.
Before passivation, the surface must be free of all interfering substances. These substances include:
Therefore, before the passivation process, a degreasing process should be carried out to remove the organic impurities such as greases, enzymes, or proteins.
The test procedures for the quality of the passive layer check whether free iron ions are present on the chromium steel surface. There are 5 different procedures for this test.
The most frequently used are:
Other test experiences are:
Multi- or strongly oxidizing acids, such as citric acid or nitric acid, are suitable for passivation. Citric acid requires a concentration of 4-10%, nitric acid a concentration of 20-25% to produce a passivating effect. Both media can be used to clean and passivate at room temperature in the above concentrations.
For disposal, both media can be slowly and gradually neutralized with caustic soda to a pH of 5.5 – 8. When nitric acid is neutralized with caustic soda, sodium nitrite is formed. Neutralization of citric acid with caustic soda produces mono to trinatron nitrite. Both neutralized applications may be disposed of in industrial wastewater at a pH between 5.5 and 8.