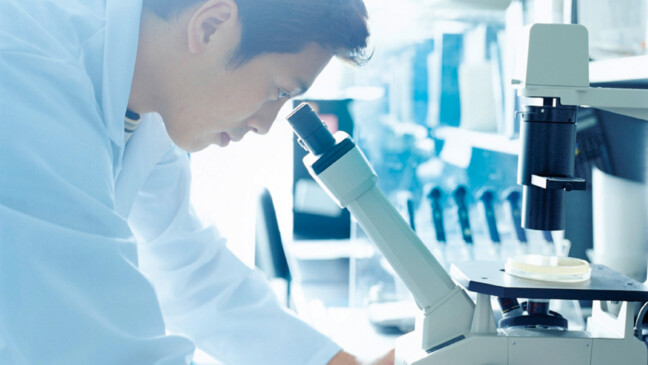
01.11.23
A cleanroom is a specially controlled work area that is kept particularly "clean" and free of contaminants such as particles, pyrogens and/or microorganisms. We explain to you what must be observed in a clean room.
Cleanrooms are typically used for sensitive or critical processes that require a very high level of cleanliness, such as the manufacture of pharmaceuticals, medical devices, electronics, semiconductors or food. Air quality in cleanrooms is continuously monitored and regulated to ensure that the cleanroom environment meets the required cleanliness standards. As a rule, people working in cleanrooms must wear special clothing and protective equipment and follow special processes to ensure the cleanliness of the environment.
In the pharmaceutical field, there are many different rules and regulations that apply to cleanrooms. These rules are constantly updated to reflect the latest science and technology. There are regulations, standards, guidelines and directives that cover all different aspects of cleanroom design and operation. These rules are important to ensure that cleanrooms meet the highest standards and ensure the safety and quality of manufactured products. ISO stands for International Organization for Standardization and GMP for Good Manufacturing Practice.
The ISO 14644 standard and GMP Annex 1 play a prominent role here. ISO 14644 specifies criteria for particle control and classification of cleanrooms, while GMP Annex 1 is part of the GMP guidelines and focuses on the control of microbiological contamination, particles as well as pyrogens in drug manufacturing. Both standards complement each other by defining requirements for microbiological measurements and particle control in cleanrooms.
In the pharmaceutical field, there are many different rules and regulations that apply to cleanrooms. These rules are constantly updated to reflect the latest science and technology. There are regulations, standards, guidelines and directives that cover all different aspects of cleanroom design and operation. These rules are important to ensure that cleanrooms meet the highest standards and ensure the safety and quality of manufactured products. ISO stands for International Organization for Standardization and GMP for Good Manufacturing Practice.
The ISO 14644 standard and GMP Annex 1 play a prominent role here. ISO 14644 specifies criteria for particle control and classification of cleanrooms, while GMP Annex 1 is part of the GMP guidelines and focuses on the control of microbiological contamination, particles as well as pyrogens in drug manufacturing. Both standards complement each other by defining requirements for microbiological measurements and particle control in cleanrooms.
Contamination means that unwanted substances or microorganisms enter and lead to contamination of the cleanroom. This can include general dirt, dust particles, bacteria, yeasts and fungi, viruses and pyrogens, but also chemical substances. Contamination can affect the quality or safety of products. In areas such as pharmaceuticals or biotechnology, contamination control plays a particularly important role in protecting consumer health and ensuring the quality of manufactured products.
There are different types of contamination that can occur in different environments:
Particulate contamination refers to the ingress of small solid particles such as dust or fibers that can contaminate the air or surfaces.
Microbial contamination involves the presence of living microorganisms such as bacteria, viruses, yeasts or fungi that can cause disease or affect product quality.
Chemical contamination occurs when undesirable non-living chemical substances, e.g., classical chemical molecules, proteins, and pyrogens, are released into the environment, which can have toxic effects or affect product integrity.
Biological contamination by macroorganisms refers to the transfer of living larger organisms such as insects or rodents that can pose a potential hazard.
Cross-contamination occurs when microorganisms, contaminants or other impurities are transferred from one surface to another. This can happen, for example, when bacteria are transferred from hands to a work surface or are transported from one location to another by air movement. In the cleanroom, it is particularly important to avoid cross-contamination, as even small contaminants can affect the quality of products. Furthermore, electrostatic charging of surfaces can lead to accumulation and adhesion of particles or to undesirable physical and chemical interactions with products or on surfaces.
In cleanrooms, humans are often the largest source of contamination. Because we naturally shed particles, microorganisms and chemical compounds, our presence in the cleanroom can lead to an increased risk of contamination. For example, dander, hair, breath or touching surfaces can cause contamination. In addition, improper handling of materials, inadequate cleaning or inappropriate hygiene measures can lead to contamination. Therefore, training of personnel in hygiene practices and the use of appropriate protective clothing is of great importance to minimize the source of contamination “humans”.
In cleanrooms, other sources of contamination besides humans may be present. These include particles or microorganisms from the environment, residues of cleaning agents and disinfectants, unsuitable materials and inadequate air filtration systems. Several measures are required to identify and minimize these sources. These include implementing effective air filtration systems, regularly reviewing cleaning and disinfection procedures, selecting appropriate materials, and monitoring environmental influences. Targeted identification and minimization of these sources can ensure the purity and quality of products in cleanrooms.
Detecting contamination can be difficult, especially when it is caused by the failure of an entire system such as ventilation, an autoclave or water treatment. In such cases, the effects are so severe that standard control systems such as ventilation monitoring and sterility testing almost always detect the various sources of contamination and its origin. This is because these systems are specifically designed to detect such serious contamination. This ensures that the products are safe and free from contamination. It is important that these control systems are implemented correctly and checked regularly to ensure a high probability of detection and to protect the quality of the products.
To minimize contamination, specific measures such as cleaning, disinfection, monitoring of environmental conditions, regular training of personnel and compliance with hygiene standards are implemented.