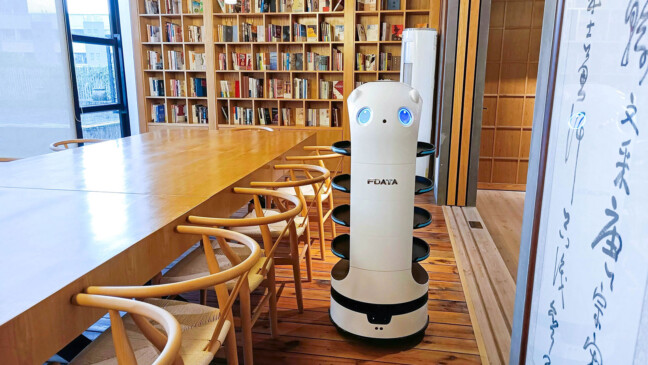
03.04.23
The pharmaceutical market offers a wide range of treatment solutions for cleaning and passivation of stainless steel pharmaceutical equipment. Their further development with the aim of achieving economic and ecological improvements has been achieved mainly by gradually changing the chemical composition of the treatment solutions.
An intact passive film is essential for the corrosion resistance of pharmaceutical equipment. However, corrosion resistance is not a material property, but depends on the material and environment of the respective corrosion system. Corrosion systems in this environment (pharmaceutical equipment made of stainless steels) are mostly electrochemical in nature. From the laws of this electrochemical nature, it is clear that in an existing corrosion system crevice corrosion always occurs as the first form of corrosion. From these findings, the existing experience is confirmed that for this group of materials, anything that is not an intact passive film can constitute a crevice. It follows from this: Cleaning, i.e., the removal of these potential gaps, is of decisive importance for an effective passive film to build up in the first place. Therefore, it is obvious to use electrochemical investigation methods to classify and optimize passivation solutions.
The pharmaceutical market offers a wide range of treatment solutions for cleaning and passivation of stainless steel pharmaceutical equipment. Their further development with the aim of achieving economic and ecological improvements has been achieved mainly by gradually changing the chemical composition of the treatment solutions. It is generally known that in this group of materials it is above all the quality of the passive film that determines whether negative influences from a surrounding medium are kept within limits. It therefore makes sense to take a closer look at the material surface in contact with the product, because mutual influences can only occur in this contact zone – also known as the phase boundary – between the material and the medium.
In surface technology, passivation is understood as the spontaneous formation or the targeted generation of a protective film, which practically prevents the corrosion of the metallic material. One of the best known technical significance of this phenomenon is the use of stainless CrNi(Mo) steels, which are mainly used in chemical and pharmaceutical industry plants. The cause of this passivity is the alloying element chromium, which must be present in the stainless steel at a mass fraction of at least 13% so that a corresponding passive film can form on the surface. This passive film forms spontaneously in a natural environment (hence: stainless steels) and is in thermodynamic equilibrium with it. Consequently, a passive film can be degraded in a different environment to such an extent that corrosion phenomena can occur. On the other hand, it can also be optimized by defined treatment to such an extent that it provides the effective corrosion protection it is intended to. Experience also shows that local types of corrosion can be initiated in particular at weak and disturbed points in the passive film, whereby this is closely linked to the presence of chloride ions in the case of stainless steels.
More precisely, stainless steels are only steels which do not form rust in moist air or in water without corrosion aggravating boundary conditions. Depending on the material composition, even more aggressive conditions are tolerated. This restriction leads to the definition of corrosion in DIN EN ISO 8044: “Corrosion is the physicochemical interaction between a metal and its environment which leads to a change in properties and which can result in significant impairment of the function of the metal, the environment or the technical system of which they form a part. This metal/environment interaction is often electrochemical in nature.” In summary, corrosion resistance is therefore not a material property, but a system property.
This mechanism is characterized by the fact that the corrosion attack occurs exclusively at the phase boundary between an electron conductor (metal) and an ion conductor (electrolyte as environment). Electrochemical corrosion involves redox reactions, the overall reaction of which can always be described in 2 partial reactions. The anodic partial reaction is the actual corrosion reaction as a metal dissolution process. This reaction corresponds to an oxidation process in which electrons are generated at the anode. For reasons of electroneutrality, this electron-supplying reaction must be opposed by an electron-consuming reaction at the cathode. The cathodic partial reaction corresponding to a reduction process controls the respective corrosion process. The two partial reactions occur simultaneously on the metal surface (with the same electron turnover, but not at one and the same point) and lead to charge separation as a result of their charge turnover. This charge separation can be measured against a defined reference as a potential.
Due to the electrochemical nature of the corrosion processes under consideration, electrochemical investigations constitute a significant element in corrosion research. Among the numerous methods, the recording of current density-potential curves in the respective corrosive environment has proven to be particularly informative for stainless steels. Additionally, fundamental relationships can be derived from the curve’s behavior.
To determine current density-potential curves, a special electrical circuit is used in an electrolyte to analyze the current density (current per unit area) as a measure of the corrosion rate in relation to a dynamically and deliberately altered potential. Usually, current-voltage curves are recorded, and both current density and potential are derived with their respective reference points. For stainless steels, characteristic and fundamentally identical curve profiles are observed in many neutral and slightly acidic electrolytes (see Figure 1). For the use of stainless steels, this implies that the choice of material must initially be made so that the material and surrounding medium system remains in the stable passive range under the given conditions (see Figure 2). Therefore, those types of materials with the broadest passive range in the respective medium exhibit the highest corrosion resistance. However, this fundamental behavior in the passive range also indicates susceptibility to changes in the system. On one hand, alterations in the medium or minor changes in the physical and chemical conditions within the medium can lead to a negative change in the curve behavior (e.g., a narrower passive range). On the other hand, weaknesses and defects in the passive film can initiate localized forms of corrosion (e.g., pitting corrosion when chloride ions are present, and the open-circuit potential Ecorr is more positive than the depassivation potential Ed; see also Figure 2).
Another electrochemical, dynamic investigative method, in which the potential is reversed upon reaching a defined current, provides additional insights into the stability of the passive range (see Figure 3). This curve behavior shows that both crevice corrosion and pitting corrosion are potential-dependent forms of corrosion that occur above specific critical potentials. The most important finding is that, in the same corrosion system, the potential above which crevice corrosion occurs is always more negative than the comparable potential at which pitting corrosion occurs. Therefore, crevice corrosion is the form of corrosion that would always occur first in a potentially existing corrosion system. Thus, the risk of crevice corrosion is always greater in a given corrosion system than that of pitting corrosion.
For equipment safety in the chemical and pharmaceutical industry, the findings mentioned so far imply that the corrosion resistance of the predominantly used stainless steels primarily depends on the presence of an intact passive film. It is well-known that any form of contamination on the surface can hinder the formation or maintenance of an intact passive film and can lead to weak or defect spots. Weak or defect spots in the passive film are predetermined as potential anodes (sites of metal dissolution = corrosion) in the inherently existing corrosion system. It is irrelevant whether these weak or defect spots are introduced during the material processing and/or in the operation of the equipment. Typical contaminants during manufacturing include heat tint, grease and oil residues, scale, grinding and welding spatter, chips, dust, and scratches. During operation, deposits, thermally induced changes in the metal surface, and mechanical damage mainly occur. Experience also teaches us that avoiding all forms of contamination during the construction and operation of technical equipment is not entirely possible, which is why a passivation solution should not only support and expedite the natural passivation mechanism already present but also possess high cleaning power against detrimental contaminants. Therefore, a passivation solution, even if it contains numerous oxidative components, cannot be effective if it is unable to remove existing contaminants and thus make the metallic surface accessible in the first place.